The path to greater efficiency, lower costs and less frustration
In times of skilled labor shortages, complex equipment technology, and increasing price pressure, many laboratories face a silent but momentous challenge: knowledge is being lost. Every day.
We recently conducted a survey of lab professionals on LinkedIn. Over 266 people participated, and the results were clear: More than 80% of respondents stated that their lab relies in some way on the knowledge of individuals. Over 50% even rated this reliance as "very strong."
These figures reflect a trend that has been sweeping across the entire laboratory landscape for years. The reasons for this are diverse—and they reinforce each other:
- Technological development is progressing rapidly: devices are becoming more complex, software solutions more powerful, and operation more sophisticated.
- The shortage of skilled workers continues to worsen. Well-trained personnel are hard to find—and even harder to retain.
- There's often no time for structured onboarding or systematic training in day-to-day operations. New colleagues learn according to the "learning by asking" principle – if at all.
In this complex situation, laboratories are increasingly becoming dangerously dependent – not on technology, but on individuals whose experience has become invaluable – and at the same time invisible.
What happens if these people are missing? Then an analysis no longer takes hours, but days. Errors aren't resolved but passed on. And problems that could actually be fixed in minutes lead to expensive downtime or unnecessary service calls.
Lack of knowledge has concrete consequences in the laboratory environment:
- Delayed lead times
- Costly downtimes
- Wrong decisions
- Overwhelming new employees
- And in the worst case: risks for patients or research results
The problem is not the commitment of the employees – but the system, which does not secure knowledge, does not document learning and does not provide a structure to make experience useful.
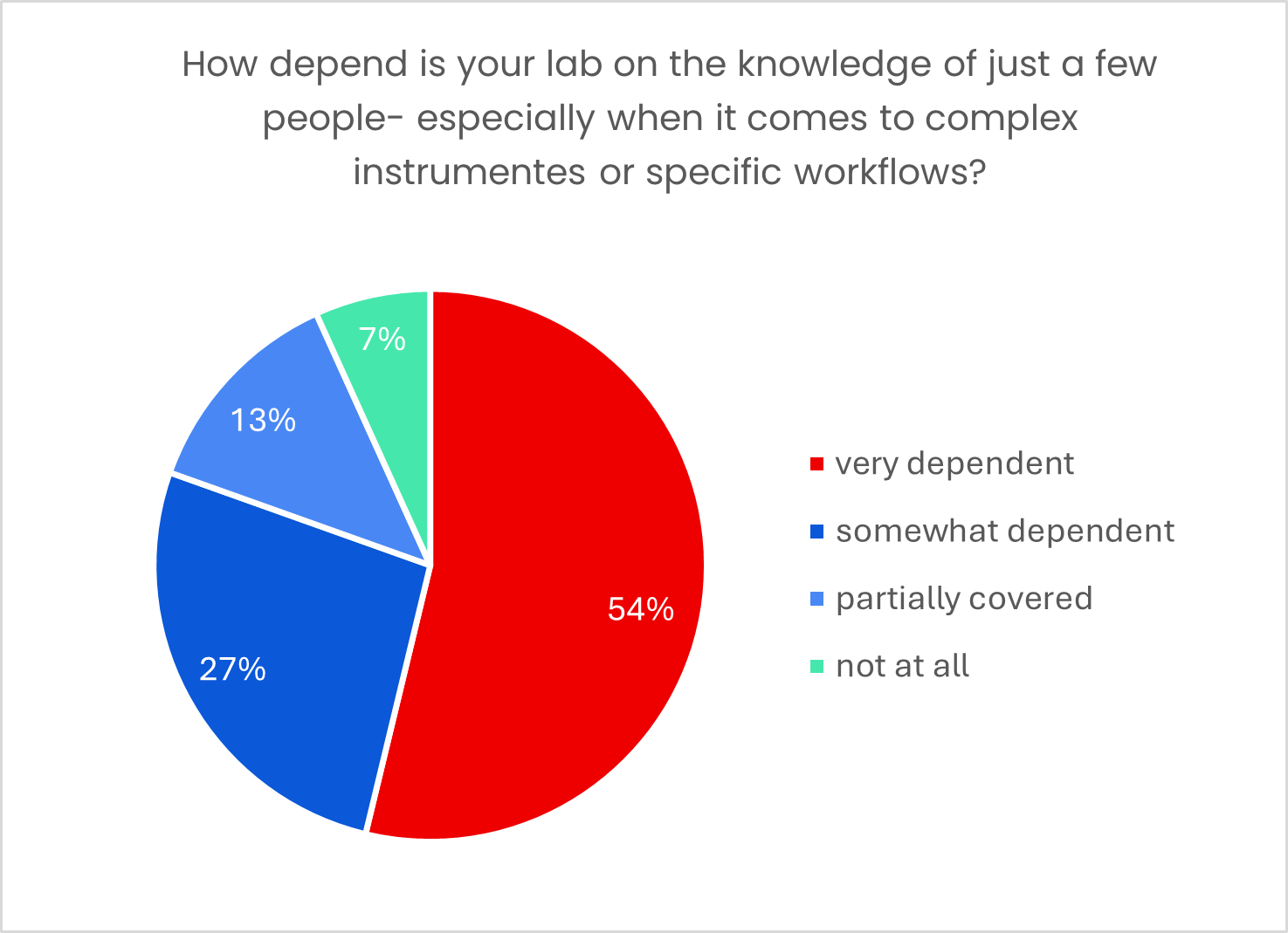
The dependence on the knowledge of individuals in the lab is alarming. Over half of the experts surveyed stated that they are highly dependent on the knowledge of individuals. (Source: LinkedIn's own survey)
The hidden costs of knowledge gaps
Knowledge gaps in the laboratory don't cause loud alarms. But they act like a creeping poison in the background: They slow down processes, block resources, and drive up costs.
A device displays an error message, but no one knows how to handle it. Instead of taking targeted action, a frustrating search for information begins – in old logs, dusty folders, or with the only person on the team who "has seen this before." If that person is unavailable, operations come to a standstill.
Such situations lead to unnecessary service calls. Errors that could be resolved internally become costly outsourcing. An on-site call can quickly cost several thousand euros – not to mention the lost time and productivity.
Without structured knowledge, training new employees takes weeks, sometimes months. The less documented experience there is, the greater the dependence on long-standing colleagues—and the resulting overload.
In addition, without clear standards and accessible empirical data, operator errors creep in. Analyses must be repeated or discarded. This can be problematic in regulated environments such as the pharmaceutical industry.
Knowledge management – a trend with substance
More and more companies are investing specifically in knowledge management systems. What was once considered an organizational accessory is now a strategic success factor. In a world of high turnover and complex processes, structured knowledge transfer is becoming a matter of survival.
Laboratories should actually take a pioneering role here. Hardly any environment is so technology-driven and so dependent on the know-how of experienced users. Even modern automation doesn't eliminate the need for understanding—in fact, it makes it all the more important.
And that's exactly where the problem lies: If nobody knows how to use technology properly, even the best technology won't help.
A typical example: Christian stands helplessly in front of a GCMS system. An error code is flashing on the display. She's holding a device manual in her hand – but it doesn't help. The colleague who knows the error is on vacation. The result: downtime, frustration, and a service call. The solution would have been known long ago – just nowhere to be found.
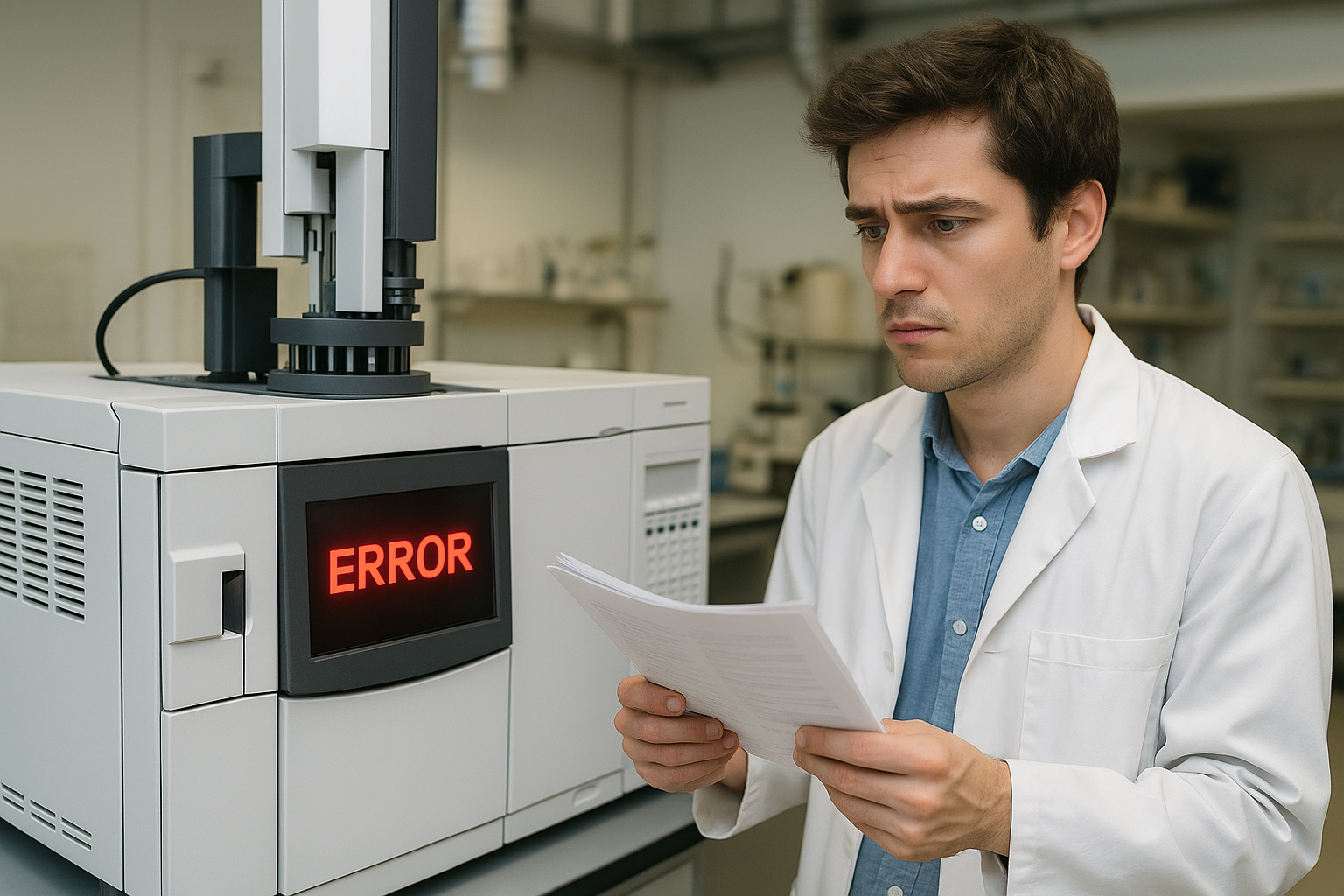
A common error. A familiar device. But no one knows what to do. Ultimately, a service technician has to come out. Costs that could have been avoided.
How AI helps make knowledge available
Manufacturers provide detailed manuals, there are videos, databases, and websites. But in practice, access at the crucial moment is often lacking. The information is scattered, difficult to search, often only available in English—and not integrated into everyday work.
This is where artificial intelligence (AI) comes in. Modern systems automatically analyze technical documents, training materials, and logbooks and provide relevant information as needed. Initial approaches—such as AI-supported PDF searches—are already showing results.
Solutions such as LabThunder® with the Thunder AI™ module go even further: They combine structured knowledge management with intelligent analysis, error detection and linguistic processing.
The AI reads manuals, training notes and operating protocols, links content with error codes and devices – and delivers the right information: in the right language, in the right context, at the right time.
The goal is not to replace experience—but to make it discoverable and usable , so that knowledge can be used where it's needed.
Conclusion: Preserving knowledge means securing the future
The laboratory world is under pressure: increasing complexity, a shortage of skilled workers, and quality requirements. At the same time, valuable empirical knowledge is disappearing every day – quietly but with significant consequences.
The development of digital knowledge management, supported by AI, is not a vision of the future – but a concrete answer to a real problem.
LabThunder® helps make knowledge permanently usable, facilitate training, minimize downtime, and relieve employee workload. Because:
A lab that preserves knowledge improves with every experience. A lab that forgets pays twice as much—in time, money, and quality.
If you would like to learn how LabThunder® can help your lab, I look forward to hearing from you.
LabThunder:
✅ Digital logbooks instead of paper chaos
✅ Thunder AI - central intelligence for faults & questions
✅ Smart & predictive maintenance prevents breakdowns
✅ More independence from external service
✅ Up to 50% fewer service calls
✅ Easy to use - no IT required
Contact us today for a free demo: